Wiring Intermittent Defect Detection
WIDD


INTERMITTENT DEFECT DETECTION
AND LOCALIZATION
Downtime, due to electrical defects, whether a full fault or an intermittent issue, in production or in the field, results in safety concerns, unscheduled maintenance, decreased asset availability and lost revenue.
The Challenge: Detecting and locating intermitent wiring faults on a vehicle quickly and effectvely, reducing downtime, minimizing labour and returning the asset to service as quickly as possible.
The Solution: Nexeya’s WiDD Series of testers.
The Approach: The WiDD Series provides an easy to use single-ended test that utlizes advanced reflectometry technology to detect and locate faults, including intermitent, with an accuracy of 1% per 100m.
Key features include:
• Portable or rack-mounted equipment
• Detecton and locaton of permanent and elusive cabling defects
• Support of all kinds of cables and harnesses
• Characterizaton and control of hundreds of points per second
• Reducton of breakdown search tmes
• Monitoring and detecton of latent faults for preventve actons
• Possibility of daisy chaining instruments for large harnesses
• Various versions and optons to meet customers’ needs
Highlighted in Airbus Technical Bulletin #58 for Airbus 320, 330, 340 with new model added on a regular basis (see pg 31).
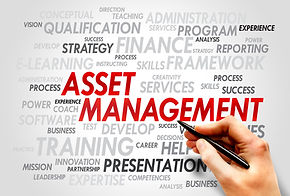
In additon to detectng and locatng defects, WiDD allows the user to characterize a harness and log changes over its life. WiDD is the only product in the market that enables life cycle material management of harnesses.